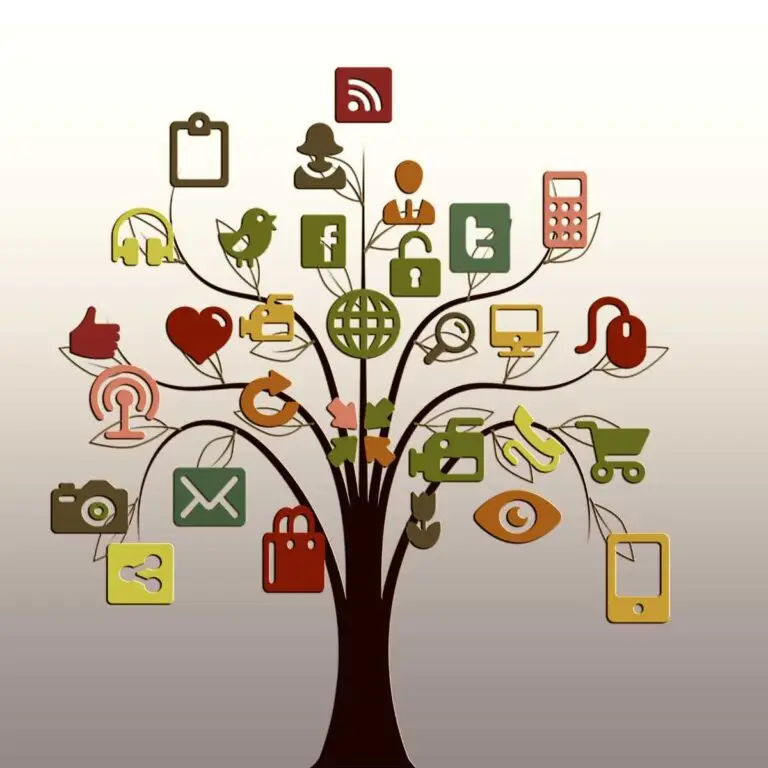
Understanding the core elements of Quality Management Systems
In today’s competitive marketplace, delivering high-quality products and services is essential for business success. A Quality Management System (QMS) is
ISO 13485 is a globally recognised Quality Management System (QMS) standard that ensures the consistent design, production, and maintenance of safe and effective medical devices. At Patient Guard, our team of experienced ISO 13485 consultants specialises in developing and implementing ISO 13485 QMSs tailored to your organisation’s needs.
Trusted by leading organisations across the UK, US & Europe
An ISO 13485 Quality Management System is a comprehensive framework designed to ensure that medical devices consistently:
In short, without it, you are limiting your market access and are liable to legal proceedings.
At its core, the goal of any QMS is to emphasise the systematic approach to identifying and mitigating risks associated with medical devices, while also striving to enhance product performance and overall patient outcomes.
Established quality management systems (QMS), such as ISO 13485, FDA regulations, and other international standards, serve as benchmarks for compliance and continuous improvement within the medical device industry.
Our ISO 13485 consultancy services encompass gap analysis, system development, training, implementation, ongoing management and support to achieve a robust ISO 13485 quality management system.
Gap Analysis and Readiness Assessment
Comprehensive gap analyses to identify compliance shortfalls in manufacturers’ quality management systems
Customised Implementation Plan
Tailored implementation plans with specific tasks, timelines, and responsibilities for achieving ISO 13485 certification
Documentation Development
ISO 13485 documentation development and refinement, ensuring quality manuals, procedures, and records are comprehensive and clear
Training and Education
Training programs on ISO 13485 principles, standards interpretation, implementation best practices, and internal auditing techniques
Process Optimisation
Process optimisation to align with ISO 13485, enhancing quality controls, risk management, and continuous improvement mechanisms
Internal Auditing and Compliance Monitoring
Conduct internal audits to evaluate the effectiveness of quality management systems and prepare manufacturers for external ISO 13485 audits
Support During External Audits
Support with documentation preparation, auditor inquiries and navigating the audit process
Post-Implementation Support
Ongoing post-certification support, including periodic reviews, documentation updates, and assistance with regulatory changes to maintain ISO 13485 compliance.
Tracey Slater, Cormed
Making sure our customers understand the type of information they need to generate to become compliant.
Removing the jargon and complexity to deliver projects that are value for money and nurture customer relationships.
Being exact, accurate and careful at all times so we deliver professional documentation.
Advice, guidance, and holding our customer's hands throughout the process from start to finish.
While not always legally mandatory, many regulatory frameworks (e.g., EU MDR, Canada, and Japan) require compliance or certification to market devices.
ISO 9001 is a general quality management system standard, while ISO 13485 is specifically tailored to the medical devices industry with a stronger emphasis on regulatory requirements and risk management.
Yes, in many cases, as certification is often a prerequisite for entering markets like the EU, Canada, and others with stringent regulations.
ISO 13485 certification is overseen by accredited certification or notified bodies. Patient Guard offers expert services to help you prepare for certification and provides ongoing support after certification.
Manufacturers, suppliers, and service providers involved in the design, production, installation, or servicing of medical devices.
Depending on the organisation’s size, complexity, and current QMS maturity, it may take 6–12 months or longer to achieve certification.
Yes, it is recognised internationally, though specific regulatory bodies may impose additional local requirements.
Yes, the standard applies to SaMD developers and requires them to demonstrate compliance with relevant lifecycle processes.
Costs vary depending on the organisation’s size, readiness, and the certifying body, including expenses for audits, training, and QMS implementation.
While not always required, some jurisdictions or markets may demand certification for even low-risk devices to demonstrate QMS adherence.
Yes, it is often integrated with standards like ISO 9001 or ISO 14971 (Risk Management for Medical Devices).
ISO 13485 was last updated in 2016. Organisations need to maintain compliance and undergo periodic audits for recertification, typically every 3 years.
In today’s competitive marketplace, delivering high-quality products and services is essential for business success. A Quality Management System (QMS) is
In today’s fast-paced and highly competitive business environment, ensuring the quality of your Medical Device products and services is paramount.
The ISO 13485 standard was built around the structure of ISO 9001 which is a standard for Quality Management Systems
Patient Guard Limited:
Lancaster House,
Amy Johnson Way,
Blackpool, Lancashire FY4 2RP
Patient Guard Europe UG:
Hauffstr. 41, 73765 Neuhausen,
Deutschland / Germany
Thank you! The checklist is now ready to download.
For help with the checklist or other aspects of your compliance journey, please reach out to us at Patient Guard and our experts would be happy to help.
UK Office