Personal Protective Equipment (PPE)
Personal Protective Equipment (PPE) plays a crucial role in safeguarding workers from potential hazards in various industries, including construction, healthcare, manufacturing, and more. PPE includes items such as gloves, helmets, eye protection, high-visibility clothing, safety footwear, and respiratory protective equipment (RPE). The effectiveness of PPE depends not only on its proper use but also on compliance with regulations that ensure the equipment meets safety standards.
In the UK and EU, there are stringent regulations that govern the use of PPE to protect workers and ensure their safety. These regulations outline the responsibilities of employers and manufacturers, and define the requirements PPE must meet to be legally sold and used in these regions.
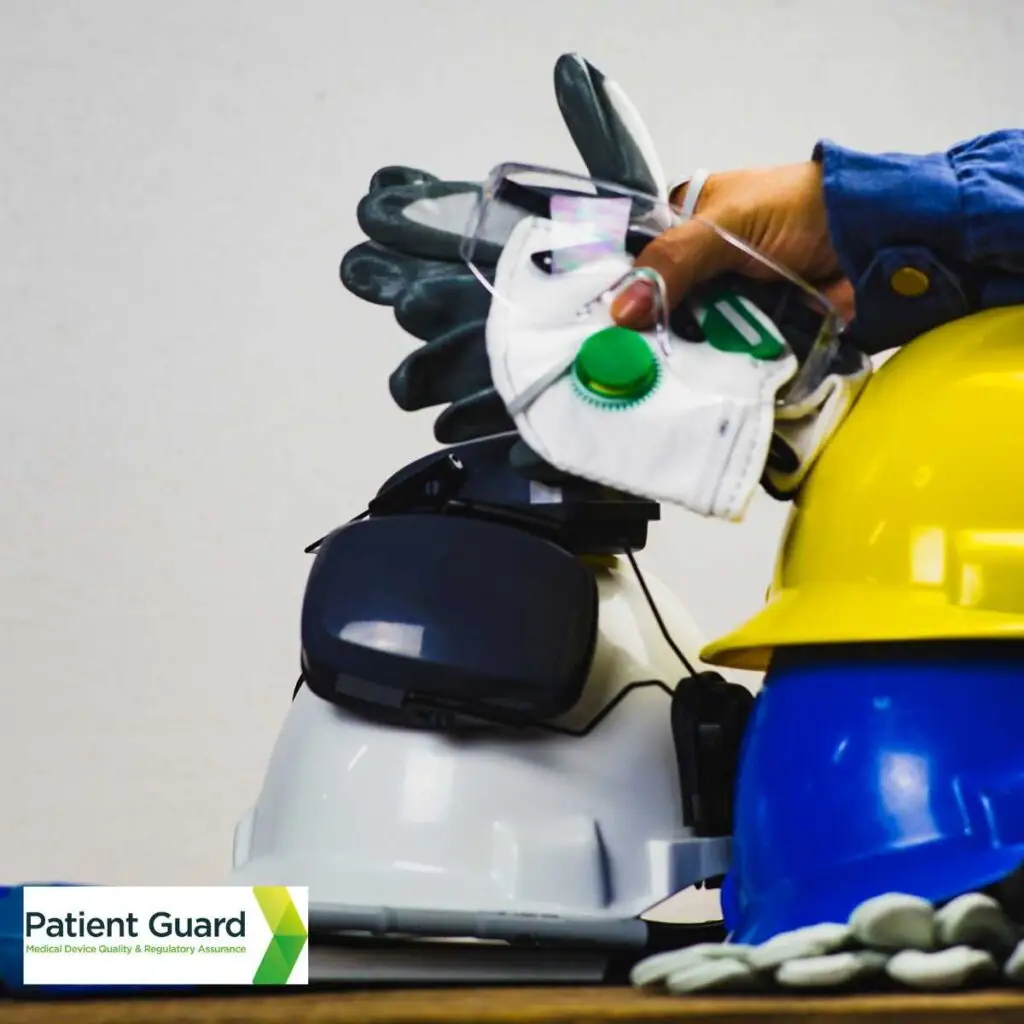
What is PPE?
PPE refers to any equipment or clothing designed to protect the wearer from workplace hazards. The specific type of PPE required varies depending on the work environment and the risks involved. For example:
- Gloves protect against chemical, biological, and mechanical risks.
- Safety helmets protect the head from falling objects and impact.
- Goggles and face shields protect the eyes and face from flying debris, splashes, and hazardous liquids.
- Respiratory protection guards against inhaling harmful substances, such as dust, vapors, and fumes.
- Foot protection ensures safety from sharp objects, chemical spills, and heavy falling objects.
While PPE is essential in many work environments, it should be seen as the last line of defence. Employers are required to first implement other controls, such as engineering solutions or safer work practices, before relying on PPE.
PPE Regulations in the UK
In the UK, PPE is regulated by The Personal Protective Equipment at Work (Amendment) Regulations 2022 and the Personal Protective Equipment Regulations 2018. These regulations place responsibilities on employers to provide PPE to workers at no cost when it is required to ensure their safety.
Employer Responsibilities:
- Assess the risks that necessitate PPE.
- Ensure PPE is appropriate for the task and fits the worker.
- Provide necessary training on the proper use of PPE.
- Maintain and replace PPE when necessary.
- Ensure PPE is CE marked, indicating it complies with health, safety, and environmental protection standards required in the UK.
Brexit Impact on UK PPE Regulations:
With the UK’s exit from the EU, certain regulatory changes have occurred. From 1 January 2021, new PPE placed on the market in Great Britain must carry the UKCA mark (UK Conformity Assessed), replacing the CE mark for most goods. However, PPE that is CE-marked can still be sold in Great Britain until the end of 2024, provided it meets EU standards. For the time being, Northern Ireland continues to use the CE marking due to its special status under the Northern Ireland Protocol.
PPE Regulations in the EU
In the EU, PPE is regulated by Regulation (EU) 2016/425, which governs the design, manufacturing, and marketing of PPE. This regulation ensures that all PPE products meet specific safety criteria before being sold in the EU.
- Key Aspects of the Regulation:
- CE Marking: All PPE sold in the EU must carry the CE mark, certifying that the product has been tested and meets the required safety standards.
- Categories of PPE: PPE is divided into three categories based on the severity of the risk it addresses:
- Category I: Simple design, for minimal risk (e.g., gardening gloves).
- Category II: Intermediate risks (e.g., helmets, protective eyewear).
- Category III: Complex design, for high-risk environments (e.g., equipment for protection against life-threatening hazards like gas masks).
- Responsibilities of Manufacturers: Manufacturers must ensure that PPE products undergo proper conformity assessments, including testing and certification by notified bodies, before being placed on the market.
- Employer Responsibilities: Under the EU framework, employers must carry out risk assessments and provide appropriate PPE based on identified hazards. Similar to the UK, PPE must be free of charge to employees, and training on its use and maintenance must be provided.
Compliance and Enforcement
In both the UK and EU, non-compliance with PPE regulations can result in enforcement actions, including fines and penalties. Regulatory bodies, such as the UK’s Health and Safety Executive (HSE) and various national authorities within EU member states, monitor and enforce compliance.
Employers are also required to regularly review their PPE needs, especially if there are changes in working conditions or new risks arise. Regular maintenance checks and prompt replacement of damaged or worn-out equipment are also mandatory.
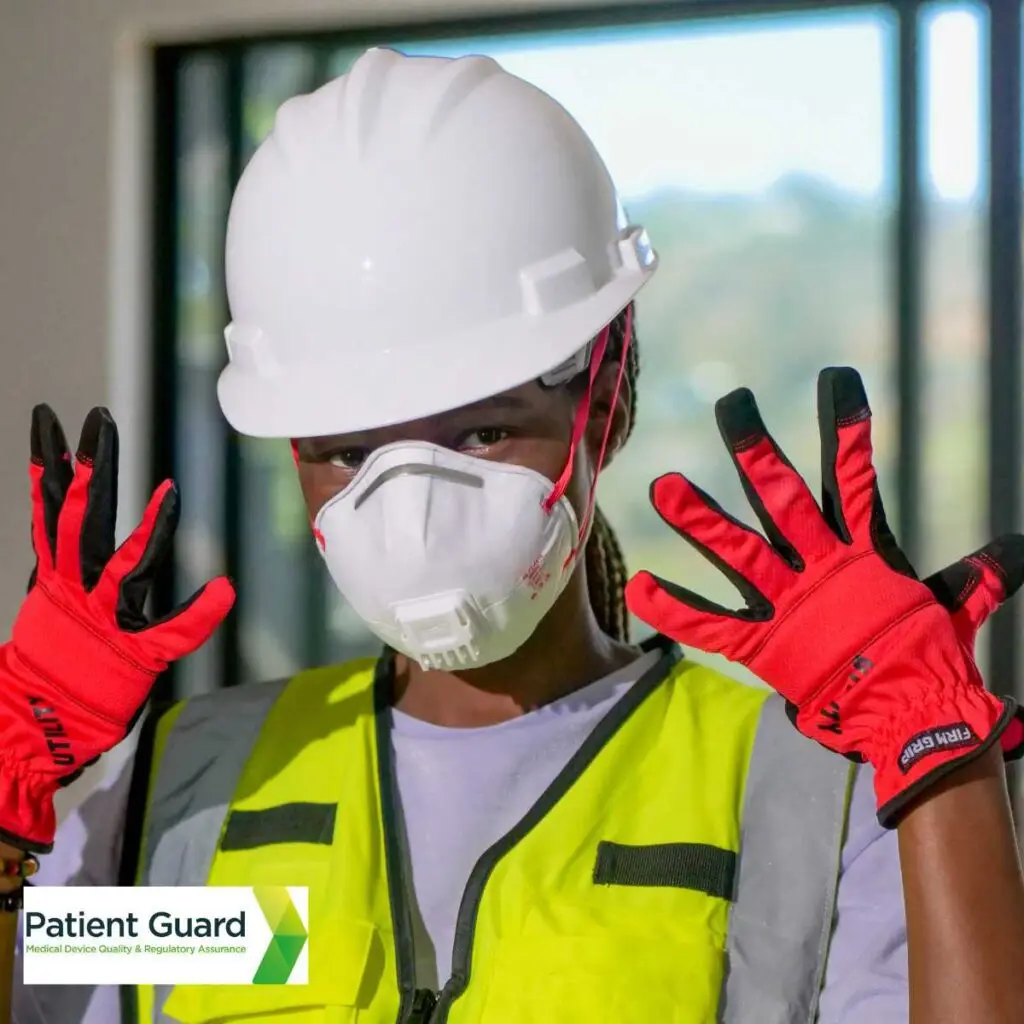
PPE Technical File Requirements
A Personal Protective Equipment (PPE) technical file is a critical document required to demonstrate that the PPE complies with relevant safety and regulatory standards. It must contain comprehensive information detailing the design, manufacturing process, and safety performance of the product. Key elements of the technical file include the product description, risk assessment, design specifications, manufacturing drawings, materials used, test reports, and evidence of conformity to relevant standards (e.g., EN or ISO standards). Additionally, it should include instructions for use, labeling details, and the Declaration of Conformity (DoC) to show that the product meets the essential health and safety requirements (EHSR). For PPE falling under Category III, which protects against very serious risks, ongoing surveillance is often required, including audits and annual testing. This technical file must be maintained and available for inspection by regulatory authorities for a defined period, typically 10 years after the last date of manufacture.
Authorised Representative
Manufacturers based outside of the EU and UK who wish to sell products within these markets are required to appoint an Authorised Representative (AR). The AR acts as a legal entity within the region, responsible for ensuring that the manufacturer’s products comply with applicable regulations, such as the EU’s CE marking requirements and the UKCA marking for the UK market. This representative handles tasks including maintaining the product’s technical file, communicating with market surveillance authorities, and facilitating the product’s registration if required. The AR is also tasked with ensuring that the product meets relevant safety standards and that proper conformity assessments have been carried out. Importantly, the manufacturer remains responsible for product safety, but the AR serves as a key liaison to ensure regulatory compliance. Failure to appoint an AR can result in the product being banned from the market.
The Future of PPE Regulation
The PPE landscape continues to evolve, especially following the COVID-19 pandemic, which highlighted the critical importance of PPE in protecting health workers and the public. Increased focus on hygiene, reusable PPE, and innovations in materials and design are likely to influence future regulations and standards. The shift towards more sustainable and eco-friendly PPE is also gaining momentum, with manufacturers exploring greener materials and recycling options for disposable PPE.
In the UK, ongoing adjustments in regulation will continue due to Brexit. Businesses and suppliers need to stay updated on UKCA marking requirements, particularly as the transition period for CE-marked products comes to an end.
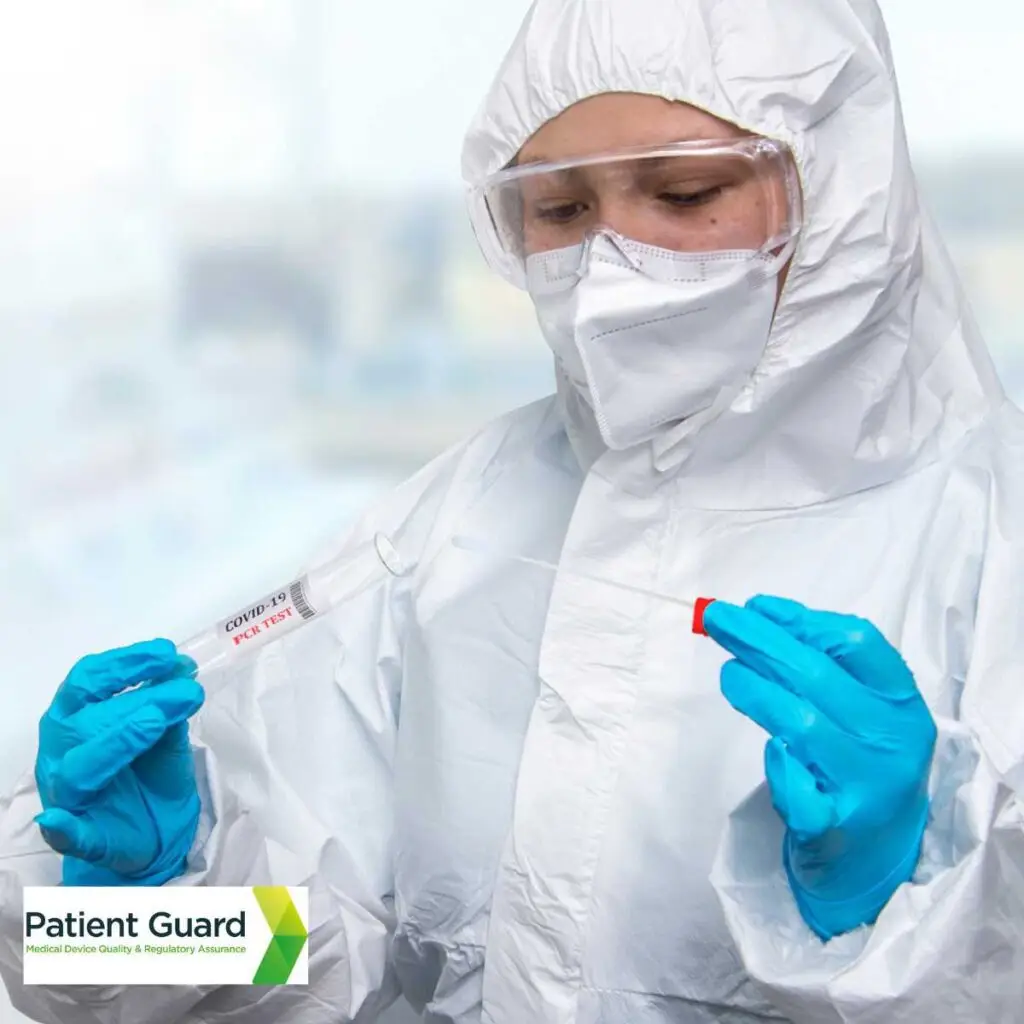
Summary
PPE is a vital component of workplace safety, and both the UK and EU have established comprehensive regulations to ensure that workers are protected from hazards. Employers have a legal duty to provide the correct PPE and ensure it meets relevant safety standards. As regulations evolve, businesses must stay informed and ensure compliance to protect both their workers and their operations.
For those in industries requiring PPE, understanding these regulations is key to maintaining a safe working environment and ensuring that protective equipment is not only suitable but legally compliant.
How can Patient Guard help?
Patient Guard is an established regulatory consultancy with expertise in both UK and EU PPE regulatory requirements. With offices in the UK and in Germany we are best place to serve as your PPE Authorised Representative. To learn more visit our PPE services page by clicking on the button below.
FAQs
Medical personal protective equipment (PPE) includes items designed to protect healthcare workers and patients from infections, biological hazards, and other risks. Examples include:
- Surgical masks
- Respirators (e.g., FFP2, FFP3 masks)
- Gloves
- Protective gowns and aprons
- Face shields and goggles
Key insight: Medical PPE must meet stringent regulatory requirements to ensure safety and effectiveness.
In the EU, medical PPE falls under two main regulatory frameworks:
- Medical Device Regulation (MDR) 2017/745: Applies if the PPE is classified as a medical device (e.g., surgical masks intended to protect the patient).
- PPE Regulation (EU) 2016/425: Covers general personal protective equipment intended to protect the user (e.g., respirators like FFP2 masks).
Pro tip: Some products, like surgical respirators, may need to comply with both MDR and PPE Regulation requirements.
In the UK, medical PPE is regulated under:
- The UK Medical Device Regulations 2002 (as amended): For products classified as medical devices.
- The UK Personal Protective Equipment Regulations 2018: For general PPE.
- UKCA Marking: Since Brexit, PPE must bear the UKCA mark to be sold in Great Britain. CE marking is still accepted in Northern Ireland under the Northern Ireland Protocol.
Key takeaway: Non-UK manufacturers must appoint a UK Responsible Person for market access.
Harmonized standards provide specific requirements for medical PPE. Examples include:
- EN 14683: For surgical masks.
- EN 149: For respiratory masks (FFP2, FFP3).
- EN 13795: For surgical gowns.
- EN 374: For protective gloves.
Compliance with these standards ensures your product meets essential safety and performance requirements.
Yes, manufacturers must implement a QMS to demonstrate regulatory compliance. Commonly used QMS standards include:
- ISO 13485: For medical devices.
- ISO 9001: For general quality management (PPE-specific).
Why it matters: A robust QMS ensures consistent product quality and facilitates regulatory approvals.
Medical PPE must include clear and compliant labeling. Requirements include:
- Manufacturer’s name and address.
- Product identification and intended use.
- CE or UKCA marking (as applicable).
- Instructions for use (IFU) in the official language(s) of the market.
- Lot or serial number for traceability.
Pro tip: Inadequate labeling is a common reason for regulatory delays—double-check before submission.
Medical PPE undergoes rigorous testing to verify compliance with safety standards. Common tests include:
- Bacterial filtration efficiency (BFE): For surgical masks.
- Particle filtration efficiency (PFE): For respirators.
- Splash resistance: For protective gowns.
- Mechanical resistance: For gloves and face shields.
Key insight: Testing must be conducted by an accredited lab to meet EU or UK requirements.
Manufacturers must monitor their products once they are on the market. Key activities include:
- Collecting user feedback.
- Investigating complaints or adverse incidents.
- Updating technical documentation as needed.
- Ensuring compliance with vigilance reporting obligations.
Best practice: Integrate post-market surveillance into your overall quality management system.
Yes, Patient Guard specializes in regulatory compliance for medical PPE in both the EU and UK. Our services include:
- Assisting with CE and UKCA marking.
- Preparing technical documentation and labeling.
- Supporting with notified or approved body certification.
- Acting as your EU Authorized Representative or UK Responsible Person.
Why choose Patient Guard: With years of experience and expertise, we ensure your medical PPE meets all regulatory requirements for seamless market entry.
Non-compliance can lead to:
- Fines and penalties from regulatory authorities.
- Removal of the product from the market.
- Damage to your brand reputation.
Key takeaway: Working with regulatory experts like Patient Guard can help avoid costly mistakes and ensure compliance.