What is Medical Device Packaging Validation?
Packaging validation is a systematic process to confirm that packaging systems meet predefined requirements and consistently perform as intended. This includes verifying that the packaging can maintain sterility, protect the device, and withstand physical stresses such as shipping and handling.
Validation activities are conducted in compliance with global standards such as ISO 11607, which outlines the requirements for packaging materials, design, and testing for terminally sterilized medical devices. The process typically involves:
- Performance Testing: Evaluating the packaging’s ability to protect the device under simulated real-world conditions.
- Sterile Barrier System Validation: Confirming the integrity of the sterile barrier system to prevent microbial contamination.
- Accelerated Aging Studies: Assessing packaging performance over the expected shelf life of the device.
- Seal Integrity Testing: Ensuring the seals of the packaging are robust and defect-free.
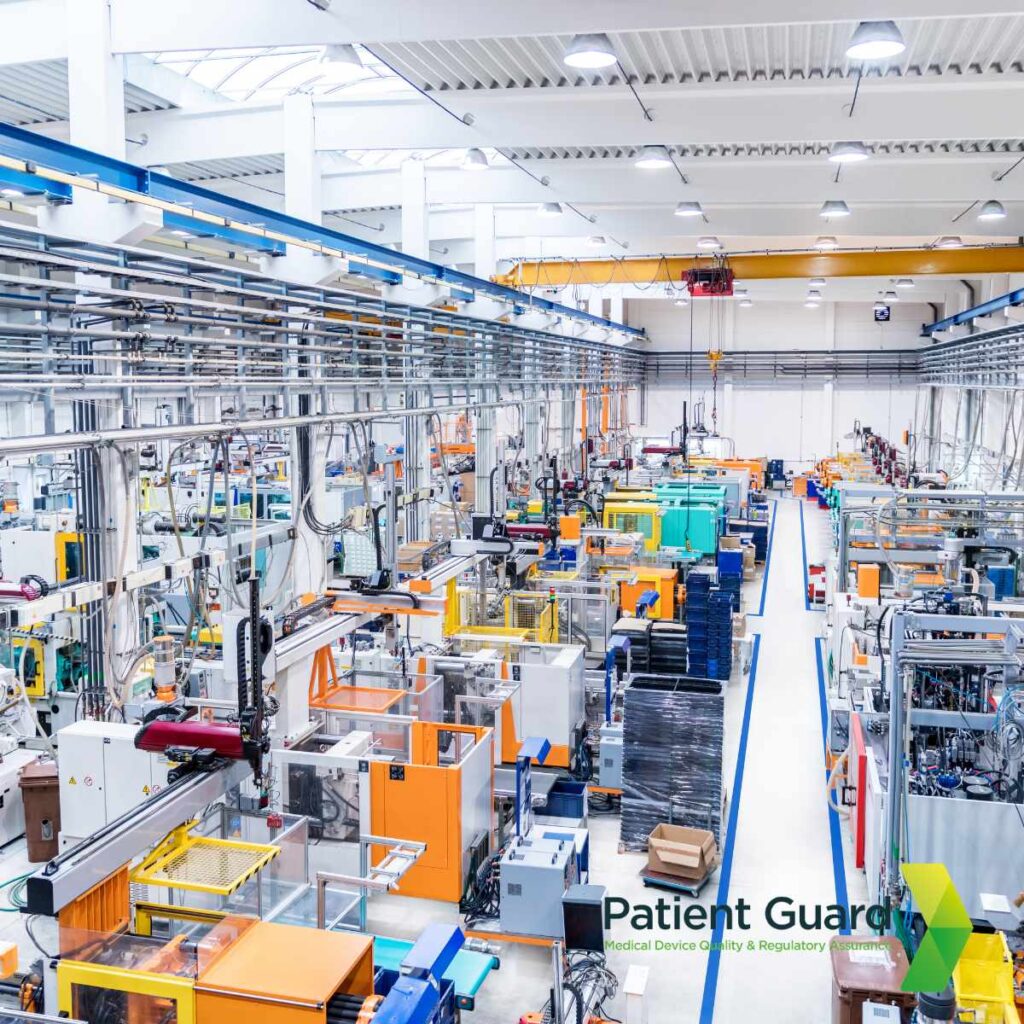
Why is Packaging Validation Essential?
Medical device packaging validation is not merely a regulatory requirement but a key factor in patient safety. Below are some critical reasons why it’s essential:
- Ensures Patient Safety: Packaging that fails to maintain sterility or integrity can lead to infections or device malfunction, directly impacting patient health.
- Regulatory Compliance: Authorities like the FDA and the European Medicines Agency (EMA) mandate strict packaging validation protocols. Non-compliance can result in penalties, product recalls, or market access denial.
- Protects Brand Reputation: Packaging failures can damage a manufacturer’s reputation and erode trust among healthcare providers and patients.
- Cost Efficiency: Early identification of packaging flaws through validation prevents costly recalls and redesigns down the line.
Key Steps in the Packaging Validation Process
1. Design Qualification (DQ):
The first step involves defining the requirements and specifications of the packaging system. This includes selecting suitable materials and designs that meet the device’s needs. The DQ process should involve risk assessment, material compatibility studies, and consideration of the device’s specific sterilization method to ensure long-term integrity and safety.
2. Installation Qualification (IQ):
IQ ensures that all packaging machinery and equipment are installed correctly and function as expected. This step involves verifying calibration, utility connections, software configurations, and operator training. IQ documentation provides a basis for ensuring that equipment operates within the specified tolerances, reducing the risk of failures in subsequent qualification stages.
3. Operational Qualification (OQ):
OQ tests the equipment’s performance under different operating conditions to confirm its reliability and repeatability. This includes testing factors such as temperature, pressure, sealing integrity, and environmental conditions. Stress testing and worst-case scenario evaluations are conducted to ensure the packaging system consistently meets performance requirements. Adjustments to process parameters may be necessary to optimize outcomes before proceeding to the next stage.
4. Performance Qualification (PQ):
PQ validates that the entire packaging process can consistently produce packaging that meets all defined specifications under real-world production conditions. This involves multiple production runs under normal working conditions to confirm consistency. Performance testing includes simulated transit studies, drop tests, and extended durability assessments to ensure the packaging maintains its integrity throughout its lifecycle
5. Ongoing Monitoring:
Once the validation process is complete, ongoing monitoring is necessary to ensure continued compliance. This includes periodic revalidation, stability testing, and routine quality control checks. If any changes occur in packaging materials, equipment, or sterilization processes, revalidation must be conducted to maintain regulatory compliance and patient safety. Continuous improvement initiatives should be implemented to optimize packaging performance and efficiency.
Challenges in Packaging Validation
Packaging validation can be a complex process due to the following factors:
- Material Compatibility: Ensuring that the selected packaging materials are compatible with the device and sterilization method.
- Global Regulatory Requirements: Navigating varying regional standards and expectations.
- Cost and Time: Validation processes can be resource-intensive, requiring careful planning and execution.
How Patient Guard Can Help
At Patient Guard, we understand the complexities of packaging validation and the stringent requirements medical device manufacturers face. Our team of experts provides tailored support, including:
- Conducting risk assessments.
- Developing and validating packaging protocols.
- Ensuring compliance with ISO, EU MDR, and FDA requirements.
Partner with us to safeguard patient safety and maintain regulatory compliance with confidence.
FAQs
The primary standard is ISO 11607, which outlines the requirements for packaging materials, sterile barrier systems, and validation processes for terminally sterilized medical devices.
The timeline for packaging validation can vary depending on the complexity of the packaging system and the scope of testing. On average, it can take several weeks to a few months, including testing, analysis, and reporting.
Accelerated aging testing helps simulate the effects of time on packaging materials within a shorter period. Learn more about accelerated aging studies. This ensures the packaging maintains its integrity and performance throughout the device’s shelf life.
Packaging validation may be reused for devices with similar characteristics, but specific assessments are necessary to confirm suitability. Any changes in the device, packaging material, or sterilization method require revalidation.
Summary
Medical device packaging validation is a cornerstone of quality assurance in the industry. By adhering to stringent validation protocols, manufacturers can ensure that their devices are delivered in optimal condition, safeguarding both patient safety and regulatory compliance.
At Patient Guard, we understand the critical importance of packaging validation. Our team of experts can guide you through the process, ensuring your packaging systems meet all relevant standards and deliver exceptional performance. Contact us today to learn how we can support your medical device’s journey from production to patient care.