Introduction
With advancements in materials and printing technologies, 3D printing is poised to become a mainstream manufacturing method in healthcare. In this blog, we explore the applications, benefits, regulatory challenges, and future potential of 3D printing in the medical device industry. We also provide best practices for compliance to help manufacturers navigate this rapidly evolving landscape.
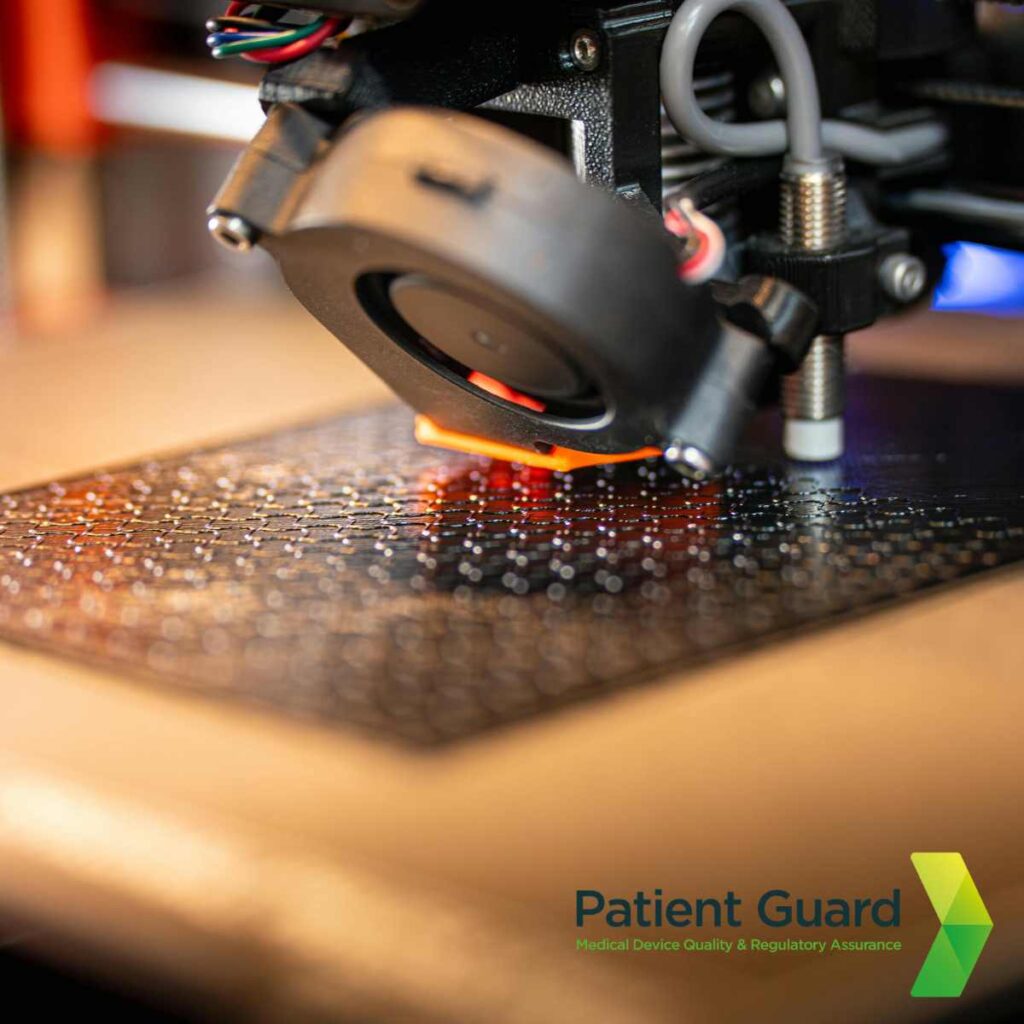
What is 3D Printing in Medical Devices?
3D printing is an additive manufacturing process that builds objects layer by layer using digital models. Unlike traditional subtractive manufacturing, which removes material from a solid block, 3D printing allows for complex designs, greater customization, and efficient material usage.
Key Types of 3D Printing Used in Medical Devices
Several types of 3D printing technologies are used in the medical device sector, including:
-
Stereolithography (SLA) – Uses a laser to cure liquid resin into solid parts, ideal for high-detail prototypes.
-
Selective Laser Sintering (SLS) – Uses a laser to fuse powdered material, commonly used for functional components.
-
Fused Deposition Modeling (FDM) – Extrudes thermoplastic material layer by layer, suitable for affordable and quick prototyping.
-
Bioprinting – Prints living cells and biomaterials to create tissue structures, a breakthrough in regenerative medicine.
Applications of 3D Printing in Medical Devices
3D printing enables the creation of highly customized and complex medical devices that would be difficult or impossible to manufacture using traditional methods. Key applications include:
1. Custom Prosthetics and Orthotics
3D printing allows for the rapid production of patient-specific prosthetic limbs, orthotic supports, and assistive devices. These devices are designed based on digital scans of a patient’s anatomy, ensuring a precise fit, improved comfort, and enhanced functionality.
2. Surgical Instruments and Guides
Surgeons can benefit from 3D-printed surgical tools and guides that enhance precision during procedures. These customized instruments reduce surgical time and improve outcomes by aligning with patient-specific anatomy. Instruments such as forceps, retractors, and scalpels can be tailored to a surgeon’s preference.
3. Implants and Bioprinting
3D printing has enabled the production of custom implants, such as cranial, dental, and orthopedic implants, designed to fit a patient’s unique anatomy. Additionally, researchers are exploring bioprinting technology to create tissue and organ scaffolds for regenerative medicine. Bioprinting could eventually enable the printing of functional organs for transplantation.
4. Anatomical Models for Training and Planning
Medical professionals use 3D-printed anatomical models to better understand complex conditions and plan intricate procedures. These models enhance surgical training and patient education, allowing for better treatment planning and improved communication between healthcare providers and patients.
5. Drug Delivery Systems
Innovations in 3D printing have led to the development of personalized drug delivery devices, such as customized pills and controlled-release medication systems tailored to a patient’s specific needs. This approach allows for precise dosages and targeted drug delivery.
Benefits of 3D Printing in Medical Device Manufacturing
The integration of 3D printing in the medical device industry offers numerous advantages:
-
Personalization: Devices can be customized to meet the unique needs of individual patients, improving treatment outcomes.
-
Faster Production: 3D printing reduces the time needed to develop prototypes and final products, accelerating the innovation cycle.
-
Cost Efficiency: Additive manufacturing minimizes material waste and reduces production costs compared to traditional manufacturing methods.
-
Improved Design Flexibility: Complex geometries and intricate designs can be easily produced, enhancing device functionality and performance.
-
On-Demand Manufacturing: Hospitals and medical facilities can produce devices on-site, reducing supply chain dependencies and improving availability.
Regulatory Considerations for 3D-Printed Medical Devices
Despite its advantages, 3D printing in the medical device industry must comply with strict regulatory requirements to ensure patient safety and efficacy. Key regulatory considerations include:
1. EU MDR Compliance
The European Medical Device Regulation (EU MDR) governs the approval and market entry of medical devices, including 3D-printed products. Manufacturers must ensure that devices meet stringent safety, performance, and risk management requirements.
2. Quality Control and Consistency
Since 3D printing involves layer-by-layer construction, ensuring consistency and reproducibility across different production batches is critical. Manufacturers must validate their processes to meet regulatory standards.
3. Material Selection and Biocompatibility
Materials used in 3D printing must be biocompatible, durable, and safe for human use. Regulatory bodies require manufacturers to demonstrate that their materials comply with medical-grade standards.
4. Traceability and Documentation
Medical device manufacturers must maintain comprehensive documentation for each 3D-printed product, including design files, material specifications, and quality control records, to ensure compliance with regulatory requirements.
Best Practices for 3D-Printed Medical Devices
To successfully navigate the regulatory landscape and optimize manufacturing, follow these best practices:
-
Perform risk assessments to identify potential hazards and mitigate them early in the design process.
-
Establish robust quality control measures to ensure consistency in printed devices.
-
Use validated and biocompatible materials that meet regulatory standards.
-
Work with regulatory experts to streamline the approval process and ensure compliance.
-
Implement traceability systems to track materials and production history for regulatory submissions.
The Future of 3D Printing in Medical Devices
The future of 3D printing in the medical device industry is promising, with continuous advancements in materials, printing techniques, and bioprinting technologies. Some potential developments include:
-
Bioprinting Human Tissues and Organs: Scientists are working on developing functional tissues and organ structures, which could eventually lead to printed organs for transplantation.
-
AI-Driven 3D Printing: Artificial intelligence and machine learning are expected to enhance the design, optimization, and automation of 3D-printed medical devices.
-
Regenerative Medicine and Personalized Healthcare: The ability to print patient-specific tissue structures could revolutionize regenerative medicine and personalized treatments.
How Patient Guard Can Help
Navigating the regulatory landscape for 3D-printed medical devices can be complex. At Patient Guard, we specialize in helping manufacturers ensure compliance with EU MDR and other global regulations. Our team provides expert guidance on technical documentation, quality management, and regulatory approvals to bring your 3D-printed medical devices to market successfully.
FAQs
3D printing offers numerous benefits, including customization for patient-specific solutions, faster production times, cost efficiency, and improved design flexibility. It also enables on-demand manufacturing, reducing dependency on traditional supply chains.
Yes, but they must comply with stringent regulatory standards such as the EU MDR. Manufacturers must ensure that materials used are biocompatible, meet quality control standards, and undergo rigorous testing before market approval.
Regulatory bodies require manufacturers to maintain strict documentation, traceability, and quality control for 3D-printed devices. Each product must meet safety, performance, and risk management requirements before receiving approval for market distribution.
The future of 3D printing includes advancements in bioprinting for tissue and organ regeneration, AI-driven design automation, and more personalized healthcare solutions. These innovations could revolutionize treatment approaches and improve patient outcomes.
Summary
3D printing is reshaping the medical device industry, offering unprecedented opportunities for customization, efficiency, and innovation. While regulatory challenges remain, the potential of this technology to improve patient care and medical outcomes is undeniable. Manufacturers must stay informed about regulatory requirements to ensure compliance and market success. If you need assistance with regulatory compliance for your 3D-printed medical device, contact Patient Guard today.
Resources
- Medical Device Labelling
- Medical Device Sterilization
- Medical Device Design and Development
- ISO 14971 and the Risk Management of Medical Devices
- The Biological Evaluation of Medical Devices
- Medical Device Cleaning Validation
-
The Internet of Medical Things (IoMT): Connecting Wearable Devices for Remote Patient Monitoring